Aerospace Resources
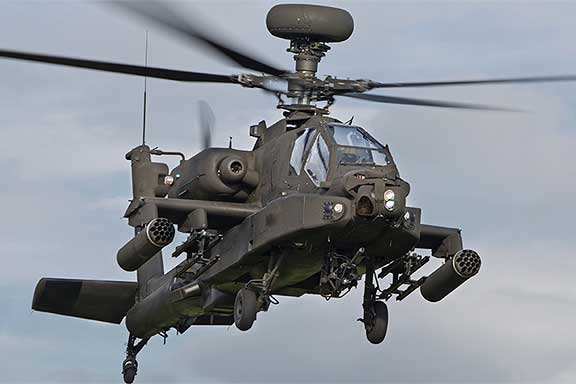
NAVAIR Awards STTR Contract to Sentient Science to Pre …
December 13, 2019 (Buffalo, NY) – The US Naval Air Systems Command (NAVAIR) has selected…
Read More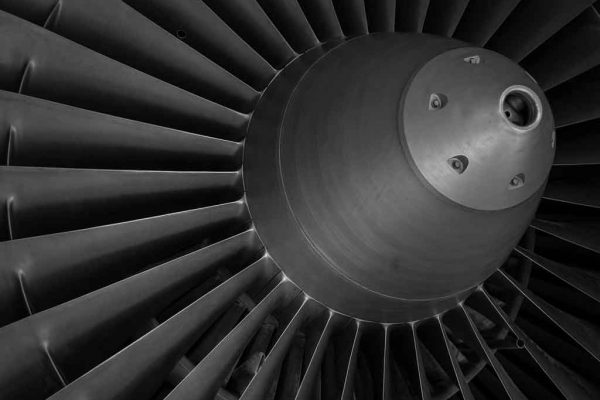
Sentient Science Announces SBIR Phase III Award from US …
September 13, 2019, Buffalo, NY – “Sentient Science has been awarded a SBIR Phase III…
Read More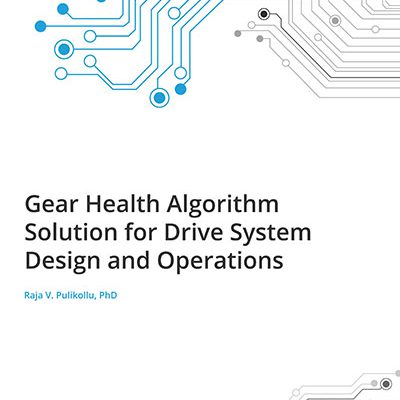
Gear Health Algorithm Solution For Drive System Design …
The safe, reliable, and efficient operation and maintenance of rotorcraft drive systems is an essential…
Read More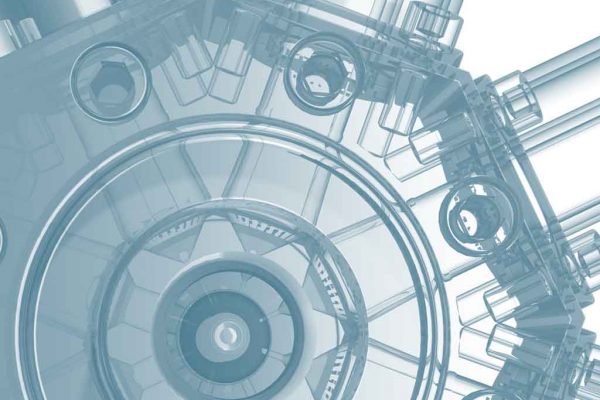
Material Sciences Based Predictive Models: A Step by St …
Dr. Raja Pulikollu, Chief Materials Scientist and Vice President of Commercial Implementations , explains Sentient Science’s…
Read More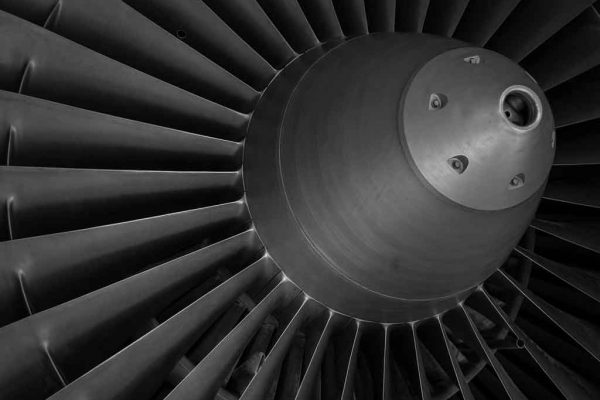
Cutting Aerospace Validation Costs in Half Using Comput …
Learn how advances in computational testing in the aerospace industry lead to reduced cost and…
Read More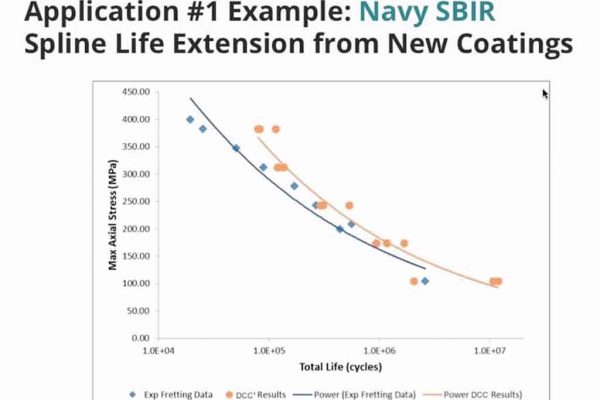
Gearbox Life Extension: Improving Rotorcraft Drivetrain …
With programs such as U.S. Army Future Vertical Lift (FVL), how can I predict rotorcraft…
Read More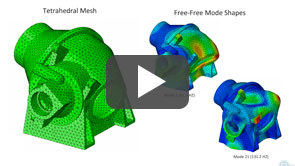
Modeling of Complex Mechanical Systems
Description: Mechanical systems, like helicopter gearboxes, are built of many complex sub-systems that require many…
Read More
A Better Approach for More Efficient, Cost Effective Ev …
Machinery testing that involves all types of equipment from airplanes to automobiles to tractors is…
Read More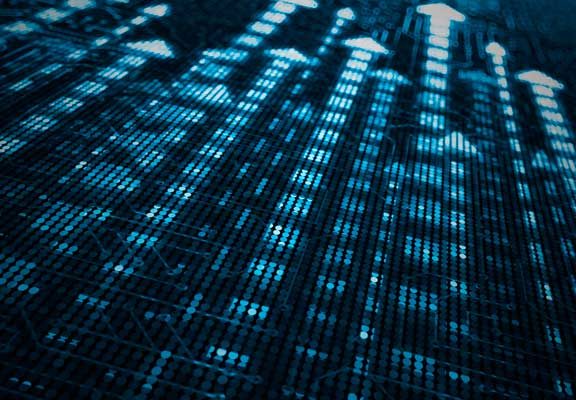
Overload Evaluation of Rotorcraft Tail Rotor Drive Spir …
This paper details an effort conducted to evaluate the effects of short to moderate duration…
Read More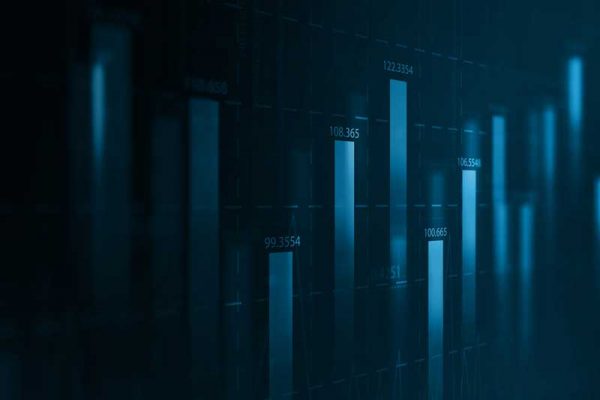
Remaining Useful Life Prediction of Helicopter Gearbox …
This paper describes an innovative approach for predicting the remaining useful life (RUL) of a…
Read More